Understanding Dip Coating Machines: Principles, Applications, and Advantages
Introduction
Dip coating is a versatile technique used to apply thin films and coatings onto various substrates by immersing them into a coating solution and then withdrawing them at a controlled rate. Dip coating are essential in industries ranging from electronics to biomedical devices due to their precision, repeatability, and ability to coat complex geometries. This article explores the principles, applications, and advantages of dip coating machines.
Principles of Dip Coating
The dip coating process involves several critical steps:
1. Immersion: The substrate is immersed in a coating solution. The depth of immersion and the duration can be adjusted based on the required coating thickness and material properties.
2. Dwell Time: The substrate remains in the solution for a specific period, allowing the coating material to adhere properly.
3. Withdrawal: The substrate is withdrawn from the solution at a controlled speed. The withdrawal speed is crucial as it determines the thickness and uniformity of the coating.
4. Drying/Curing: The coated substrate is dried or cured to solidify the coating. This step may involve ambient drying, heat curing, or UV curing depending on the coating material.
Components of a Dip Coating Machine
1. Coating Tank: Contains the coating solution. The tank can be made from various materials such as stainless steel or glass, depending on the chemical properties of the coating solution.
2. Substrate Holder: Holds and manipulates the substrate during the coating process. It can be customized to accommodate different substrate shapes and sizes.
3. Withdrawal Mechanism: Controls the speed and angle at which the substrate is withdrawn from the coating solution. This mechanism is typically programmable to achieve precise control over the coating thickness.
4. Drying/Curing System: Ensures the proper solidification of the coating. This can include ambient drying chambers, ovens, or UV curing units.
5. Control System: A programmable interface that allows operators to set and monitor various parameters such as immersion depth, dwell time, withdrawal speed, and drying/curing conditions.
Applications of Dip Coating Machines
1. Electronics: Dip coating is used to apply insulating or conductive coatings on electronic components, circuit boards, and sensors. It ensures uniform coverage and protection against environmental factors.
2. Optics: Optical lenses and mirrors are coated using dip coating to enhance properties like anti-reflective characteristics and scratch resistance.
3. Biomedical Devices: Medical implants, catheters, and stents are often dip-coated with biocompatible or drug-eluting materials to improve performance and patient outcomes.
4. Automotive: Dip coating is used for applying protective and functional coatings on automotive parts, including corrosion-resistant coatings and lubricious films.
5. Textiles: Fabrics and textiles are dip-coated to impart water resistance, antimicrobial properties, or flame retardancy.
6. Research and Development: Dip coating is widely used in laboratories for creating thin films and coatings for various research applications, including the development of new materials and nanotechnology.
Advantages of Dip Coating Machines
1. Uniform Coating: Dip coating provides highly uniform coatings, even on complex geometries, which is critical for applications requiring precise control over coating thickness.
2. Scalability: The process can be easily scaled from small laboratory setups to large industrial production lines, making it suitable for both R&D and mass production.
3. Cost-Effectiveness: Dip coating is generally more cost-effective compared to other coating techniques like spray coating or vapor deposition, especially for large or irregularly shaped substrates.
4. Versatility: Dip coating machines can handle a wide range of coating materials, including polymers, ceramics, and metals, making them adaptable to various industry requirements.
5. Ease of Use: Modern dip coating machines are equipped with programmable control systems that allow for easy operation, precise parameter control, and repeatability.
Challenges and Considerations
1. Solution Stability: Maintaining the stability and homogeneity of the coating solution is crucial for consistent results. Solvent evaporation, sedimentation, and contamination can affect the coating quality.
2. Withdrawal Speed Control: Precise control over the withdrawal speed is essential to achieve the desired coating thickness and uniformity. Variations in speed can lead to defects such as streaks or uneven layers.
3. Drying and Curing Conditions: The drying or curing process must be carefully controlled to prevent defects like cracking, peeling, or incomplete curing. The choice of drying method depends on the coating material and substrate properties.
Conclusion
Dip coating machines are indispensable tools in various industries due to their ability to produce uniform, high-quality coatings on a wide range of substrates. By understanding the principles, applications, and advantages of dip coating, manufacturers can optimize their processes to achieve superior performance and cost efficiency. As technology advances, dip coating techniques continue to evolve, opening new possibilities for innovation and application in emerging fields.
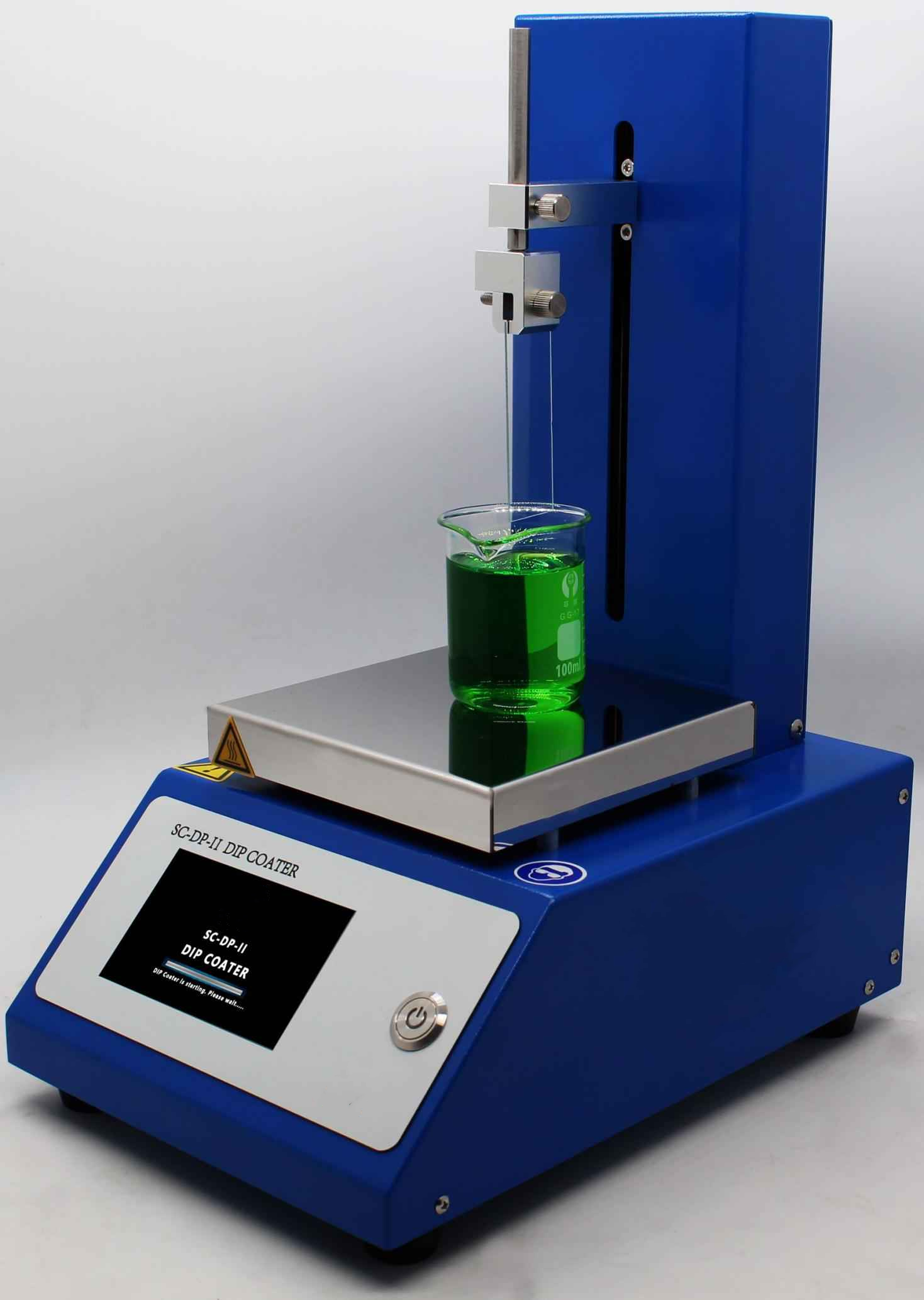